Braskem Announces University Winners for its New 3D Dimensions Design Competition
The New 3D DimensionsTM Powered by Braskem Design Competition provides an innovative forum for the next generation of 3D printing design leaders
The New 3D DimensionsTM Powered by Braskem Design Competition provides an innovative forum for the next generation of 3D printing design leaders
Philadelphia, PA - June9, 2022 - Braskem (B3: BRKM3, BRKM5, and BRKM6; LATIBEX: XBRK; OTC: BRKMY), the largest polyolefins producer in the Americas, as well as a market leader and pioneer producer of biopolymers on an industrial scale announced today the winners for the New 3D DimensionsTM powered by Braskem design competition.
In its inaugural year, the competition received a strong turnout from universities and colleges across the nation, and 18 teams made it to round two. An esteemed slate of judges reviewed submissions from a competitive pool of applicants who created designs based on one of two categories (1) Industrial Applications for Aerospace & Transportation and (2) Quality of Life for Mobility & Medical, with both categories aimed at aiding the development of the next generation of sustainable and innovative 3D printed designs. Braskem invited students from California Polytechnic State University, Virginia Tech, Carnegie Mellon University, and Penn State University to compete for cash prizes for best design.
"We are proud of everyone who participated in our first edition of New 3D DimensionsTM powered by Braskem. It was great to witness the creative and inspirational designs from all the students. The students submitted innovative ideas that have the potential to set the standard for the future of 3D printing," said Mark Nikolich, CEO, Braskem America. "I'd like to congratulate our winners. We hope you continue to bring your ideas to life, and we look forward to seeing what you accomplish in the coming years."
Judges for Braskem's New 3D DimensionsTM powered by Braskem design competition include:
- Jake Fallon - Braskem 3D Printing Material Engineer
- Haleyanne Freedman - M. Holland, Global Engineering Market Manager - Additive Manufacturing
- Dylan George - Ultimaker, Application Engineering Manager
- Adam Hecht - DiveDesign, Co-founder
- Eric Welch - The Franklin Institute, Director of Experiences
- Guénaël Morvan - nTopology, Application Engineer
- Michelle Sing - Braskem, Technology Development Engineer
Awards were presented for first, second, and third place in each design category. The first-place teams will receive $10,000, second place teams will receive $5,000, and third place teams will receive $2,500. This year's winning teams were all from Virginia Tech.
Industrial Applications for Aerospace & Transportation
1st Place: Matthew Stuart
Concept: 3D Printed Supercharger for internal combustion engine
Material: Braskem FL900PP-CF Carbon Fiber Reinforced Polypropylene Filament
Use Case: Low cost durable design, that is 100% customizable based on the size of the engine. The design was tested on a standard push lawn mower, resulting in up to a 10% increase in horsepower on small scale internal combustion engine
Benefits : low cost, customizable, lightweight, durable, low warpage, dimensional tolerances
2nd Place: Lukas Brokamp and Kamden Shephard
Concept: 3D Printed Compliant Longboard Truck
Material: Braskem FL105PP Polypropylene Filament
Use Case: Re-imagine a traditional longboard truck utilizing additive manufacturing and utilize the key benefits of polypropylene filament such as elasticity, durability, light weighting, and low cost.
Benefits : low cost, customizable, lightweight, durable, low warpage, dimensional tolerances, elasticity of material
3rd Place: Arit Das, Yimin Yao, Justin Anderson, and Martin Etemadi
Concept: 3D Printed Aftermarket Car Headlight Housing
Material: Braskem FL900PP-CF Carbon Fiber Reinforced Polypropylene Filament
Use Case: Demonstrate the value of additive manufacturing in the production of obsolete spare parts for the automotive industry or for rural communities where it is difficult to make inventory available. The team successfully replicated a factory headlight housing for a leading auto manufacturer to the exact original design specifications.
Benefits : lightweight, durable, fiber reinforced, low warpage, dimensional tolerances
Quality of Life for Mobility & Medical
1st Place: Joshua McLevain and Chase Basham
Concept: 3D Printed Modular Prosthetic Device
Material: Braskem FL105PP Polypropylene Filament
Use Case: Produce a low-cost, modular prosthetic that highlights the benefits of Braskem Polypropylene filament. A standard socket for the amputated limb was designed with two modular attachments one for driving and one for biking.
Benefits: low cost, customizable fit, lightweight, durable, chemical resistance to standard bleaches and cleaners
2nd Place: Juliana Iacono
Concept: 3D Printed Inspirational Characters for Pulse Oximeters
Material: Braskem FL105PP Polypropylene Filament
Use Case : 3D printed inspirational characters that snap onto pulse oximeters. This product was developed for children who are in the hospital to help create a more inviting atmosphere during difficult times. Regardless of how sad or scared they are feeling, they will always have their hero at their fingertip
Benefits : low cost, customizable fit, lightweight, durable, chemical resistance to standard bleaches and cleaners
3rd Place: Atlas Vernier
Concept: 3D Printed Polypropylene Wrist Braces
Material: Braskem FL105PP Polypropylene Filament
Use Case : Create a durable, lightweight, low cost, and chemically resistant 3D printed wrist brace that can be custom fit that can be quickly customized to unique body types and sizes.
Benefits : low cost, customizable fit, lightweight, durable, chemical resistance to standard bleaches and cleaners
The next edition of the design competition will launch later this year. For more information on the New 3D DimensionsTM powered by Braskem design competition please visit www.braskem.com/3daward .
ABOUT BRASKEM
With a global vision of the future oriented towards people and sustainability, Braskem is committed to contributing to the value chain for strengthening the Circular Economy. The petrochemical company's almost 8,000 team members dedicate themselves every day to improve people's lives through sustainable chemicals and plastics solutions. Braskem has an innovative DNA and a comprehensive portfolio of plastic resins and chemical products for diverse segments, such as food packaging, construction, manufacturing, automotive, agribusiness, healthcare, and hygiene, among others. With 41 industrial units in Brazil, the United States, Mexico, and Germany, Braskem exports its products to clients in more than 71 countries.
Braskem America is an indirect wholly owned subsidiary of Braskem S.A. headquartered in Philadelphia. The company is the leading producer of polypropylene in the United States, with six production plants located in Texas, Pennsylvania and West Virginia, an Innovation and Technology Center in Pittsburgh, and operations in Boston focused on leveraging groundbreaking developments in biotechnology and advanced materials. For more information, visit www.braskem.com/usa .
For press information, please contact:
Braskem North America
Stacy Torpey - (215) 841 3194 - stacy.torpey@braskem.com
Related News
Press Releases
More news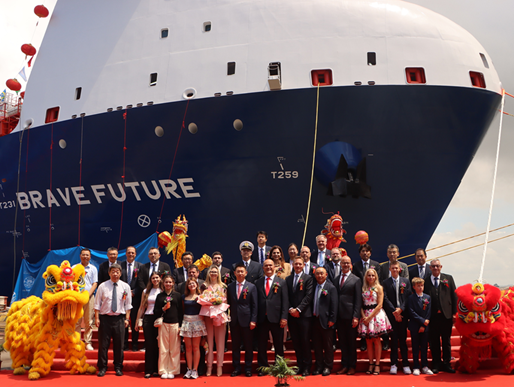
Braskem Expands Its Own Fleet with the Vessel Brave Future and Strengthens its Global Logistics Strategy
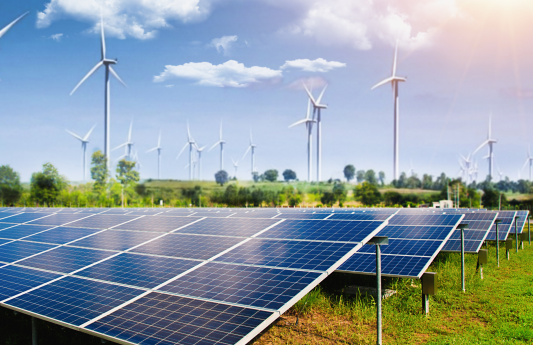
Update on Upsyde

Braskem and Ardent Advance Breakthrough Olefin Separation Technology Towards Commercial Implementation
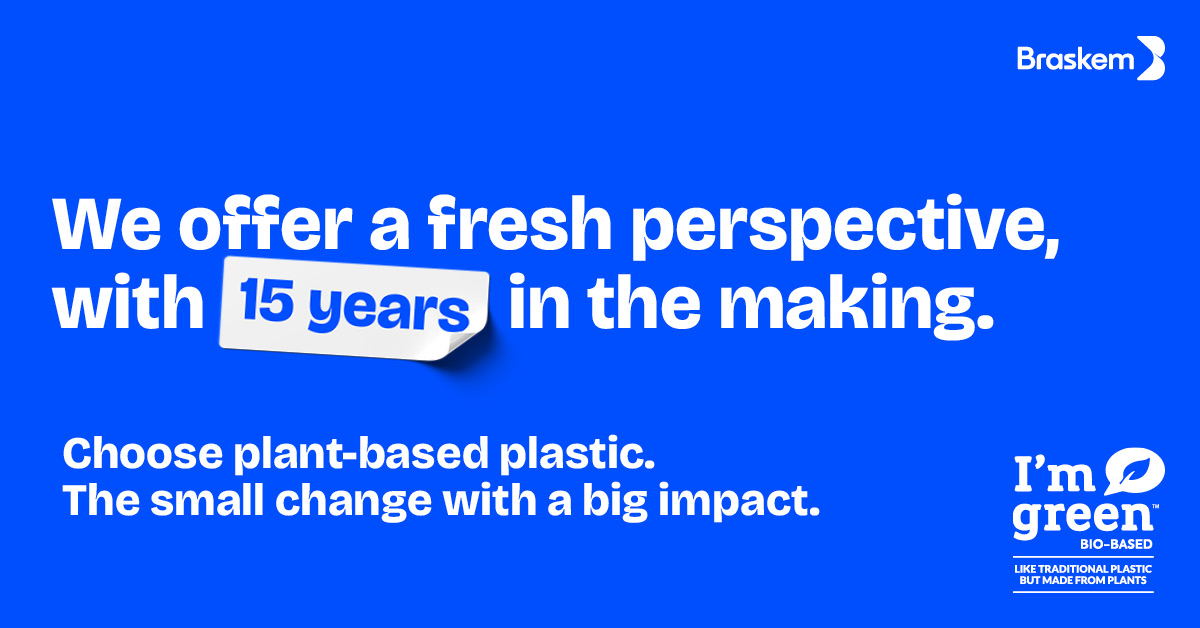
Celebrating 15 Years of I'm green bio-based with operation rates above nameplate capacity after expansion
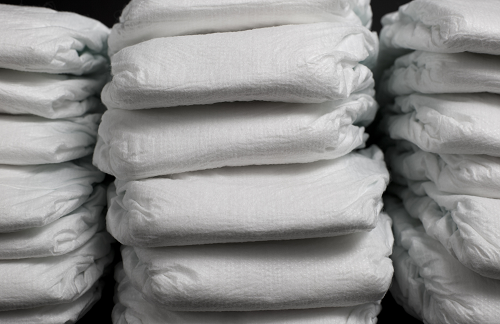
Braskem and Fitesa Announce the use of Braskem's I'm green Bio-Based Polyethylene Grade for Fitesa's Nonwovens
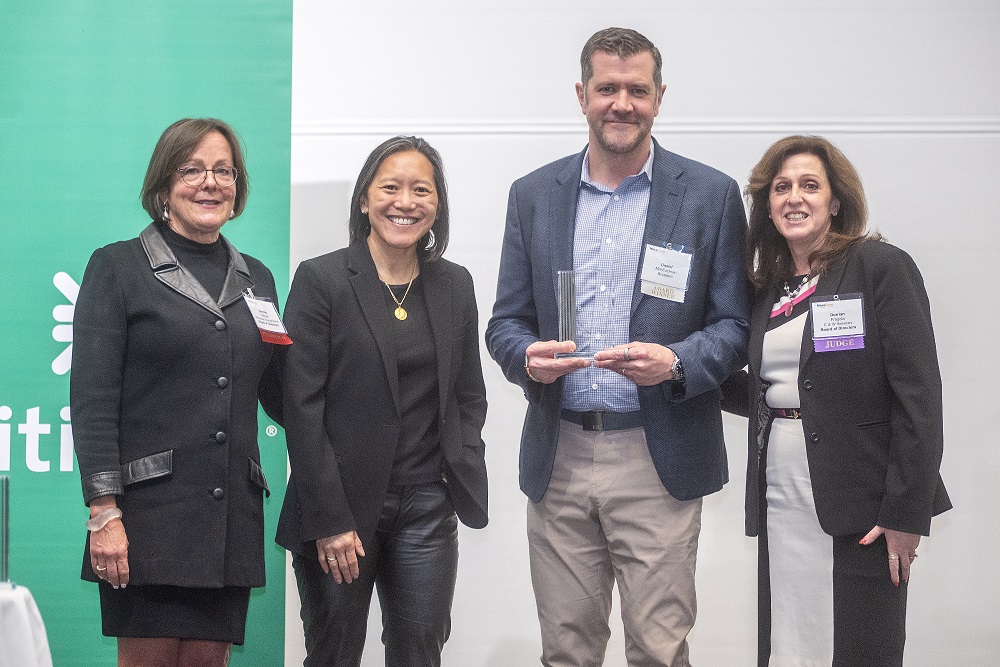