Página não encontrada
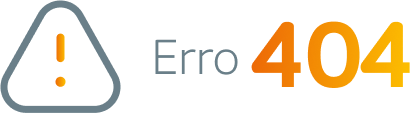
A página pode ter sido removida ou o endereço está incorreto.
Voltar para a HomeA página pode ter sido removida ou o endereço está incorreto.
Voltar para a HomeUtilizamos cookies para que você tenha a melhor experiência do nosso site. Por sua visita contínua ao nosso site, sem alterar suas configurações, você concorda com o uso de cookies da Braskem.
Sim, aceito cookies Alterar configurações de cookies Mais informações
Você pode alterar as configurações de cookies ativando ou desativando os cookies analíticos e de terceiros aqui. Você não pode desativar os cookies estritamente necessários. Você pode descobrir mais sobre cookies aqui.
Observe que alguns recursos do site não funcionarão sem cookies.
Cookies estritamente necessários
Esses cookies são essenciais para sites e para que seus recursos funcionem corretamente. Sem esses cookies, certos serviços podem ser desativados.
Cookies analíticos
Esses cookies coletam informações sobre como você usa o site e nos permitem mapear o comportamento de visitantes e pesquisas e ajustar nossos serviços de acordo com as descobertas. Isso nos permite melhorar ainda mais nossos serviços para você como visitante. Usamos cookies analíticos, como o Google Analytics.
Cookies de terceiros
Esses cookies são instalados por terceiros, por exemplo, redes sociais. Seu principal objetivo é integrar o conteúdo de mídia social em nosso site, como plug-ins sociais.